Understanding Split Flange Caps and Plugs: Key Components in Modern Fittings
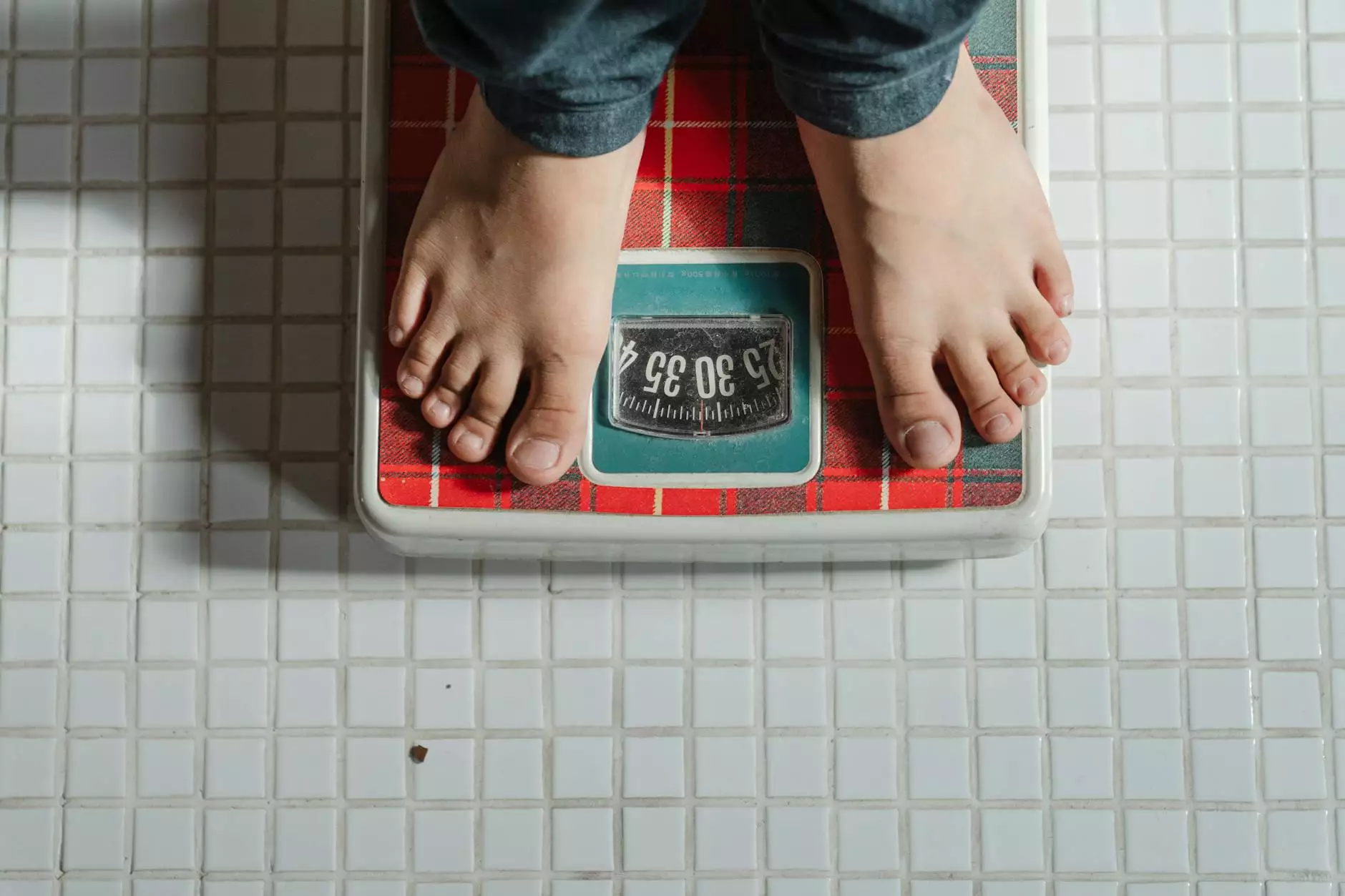
In the world of industrial fittings, split flange caps and plugs play a critical role in ensuring the integrity and reliability of connections. Their design and functionality are uniquely suited to meet the demands of various applications, from manufacturing to construction. This article delves into the features, benefits, and best practices associated with using these essential components, highlighting why they should be included in any project involving fittings.
What Are Split Flange Caps and Plugs?
Split flange caps and plugs are specialized components designed for use with flanged fittings in piping systems. They provide a reliable and secure way to seal and protect the ends of pipes or connections from environmental hazards, debris, and contamination. This is particularly important in industries where cleanliness and safety are paramount, such as in chemical processing, food and beverage manufacturing, and pharmaceuticals.
The Anatomy of Split Flange Caps and Plugs
These components can be broken down into several key parts:
- Flange Body: The primary part that fits flush against the fixed flange.
- Splits: These are the notches or cuts made in the flange body that allow for flexibility and ease of installation.
- Sealing Mechanism: Often incorporates gaskets or O-rings to ensure a tight seal.
Understanding these parts is crucial for selecting the right split flange caps and plugs for your specific needs.
Why Choose Split Flange Caps and Plugs?
There are numerous reasons why split flange caps and plugs are favored in various industries:
1. Enhanced Protection
One of the primary benefits of using split flange caps and plugs is their ability to protect the interior of pipes from dust, debris, and moisture. By providing a robust seal, these components prevent contamination which is crucial for maintaining the quality of the media within the pipes.
2. Easy Installation and Removal
The split design of these fittings allows for quick installation and removal. This is particularly advantageous in situations where frequent maintenance or inspections are required. Users can easily cap or uncross the connections without the need for specialized tools.
3. Versatility in Applications
Split flange caps and plugs are not limited to one specific industry or application. They can be used effectively across various domains, including:
- Oil and Gas
- Chemical Processing
- Water Treatment
- Pharmaceuticals
- Food and Beverage
4. Cost-Effectiveness
Investing in split flange caps and plugs can lead to significant cost savings over time. By preventing leaks, spills, and contamination, these components can reduce the need for costly repairs, compliance fines, and product losses.
Choosing the Right Split Flange Caps and Plugs
When it comes to selecting the appropriate split flange caps and plugs, consideration of various factors is essential:
1. Material Selection
These fittings are made from different materials, including:
- Stainless Steel: Highly resistant to corrosion and suitable for harsh environments.
- Plastic: Lightweight and cost-effective for non-critical applications.
- Aluminum: Offers good strength-to-weight ratio and corrosion resistance.
Your specific use case will dictate the best material choice for your needs.
2. Sizing and Compatibility
Ensuring that the split flange caps and plugs you choose are compatible with your existing fittings is essential. Pay close attention to:
- Diameter
- Flange thickness
- Pressure ratings
3. Environmental Considerations
Consider the environmental conditions in which the fittings will be used. Factors such as temperature, pressure, and exposure to chemicals can greatly influence the performance of the split flange caps and plugs.
Installation Best Practices for Split Flange Caps and Plugs
Proper installation is key to ensuring the effectiveness of split flange caps and plugs. Here are some best practices to follow:
1. Clean the Flange Surface
Before installation, ensure that the flange surfaces are clean and free from debris. This will help to provide a better seal and prevent leaks.
2. Inspect the Components
Always inspect the split flange caps and plugs for any signs of damage or wear. Compromised components should be replaced to avoid issues in the future.
3. Proper Seating
During installation, ensure that the cap or plug is properly seated against the flange. This ensures a secure fit and optimal sealing.
4. Use Proper Torque Settings
When applying bolts or fasteners, adhere to the manufacturer's specifications regarding torque settings. Over-tightening can lead to damage, while under-tightening may result in leaks.
Common Applications of Split Flange Caps and Plugs
Split flange caps and plugs are utilized in various industries for multiple applications:
1. Oil and Gas Pipelines
In the oil and gas sector, these fittings provide secure closures for pipelines, safeguarding the transport of volatile substances. Their durability and resistance to varying pressures make them ideal for this critical industry.
2. Chemical Storage and Processing
Split flange caps and plugs are essential for safe chemical handling. They prevent environmental contamination and maintain the integrity of stored substances.
3. Pharmaceutical Manufacturing
In pharmaceutical settings, cleanliness and sterility are of utmost importance. These fittings provide the necessary protection to avoid contamination during processing and storage.
Maintaining Split Flange Caps and Plugs
Regular maintenance of split flange caps and plugs can enhance their longevity and functionality:
1. Routine Inspections
Conduct routine visual inspections to identify any signs of wear, damage, or corrosion.
2. Cleaning
Ensure that the components are kept clean and free from abrasive materials that could damage their surfaces.
3. Replacement Schedule
Establish a replacement schedule based on usage and environmental conditions, ensuring that worn components are swapped out before they fail.
Conclusion: The Importance of Quality in Fittings
The significance of split flange caps and plugs in industrial applications cannot be overstated. Quality, durability, and functionality are crucial for ensuring safety and efficiency in operations. By understanding the role these components play and by adhering to best practices in installation and maintenance, businesses can protect their systems, reduce costs, and enhance productivity.
If you are seeking high-quality fittings for your business needs, look no further than fitsch.cn. Their commitment to excellence and extensive range of products, including split flange caps and plugs, positions them as a leader in the field.